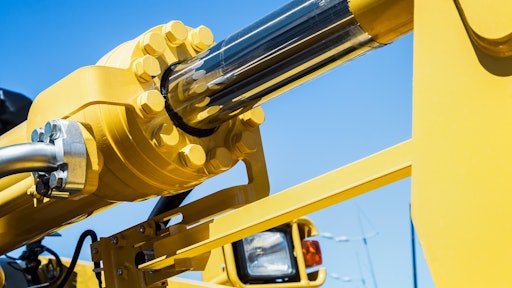
液压油的核心是在设备中执行两个关键功能。首先,它们必须能够在机器部件之间传输电力。其次,他们还必须保护设备的组件,这可以降低车队所有者的总拥有成本(TCO)。
然而,精明的设备技术人员意识到,适当配方的液压油提供的功能远远超出这两个核心标准。它们可以防止硬件过度磨损。它们最大限度地减少热降解和氧化降解。它们可以减缓机器部件的污染和污泥积聚。它们可以防止生锈和腐蚀,减少摩擦和散热。换句话说,设计良好的液压油对于保持设备在油的整个生命周期内以最佳性能运行至关重要。
那么,操作人员如何决定哪种液压油最适合设备的运行参数呢?通常,他们依赖于润滑油制造商和石油营销人员提供给他们的信息。为此,重要的是在最相关的条件下测试液压油,以提供流体在实际设备中如何表现的准确信息。
从历史上看,预测油的寿命是通过两个标准的氧化稳定性台架试验来收集的。但随着设备的发展,液压油的工作条件也在不断变化,而相关测试并不一定能准确反映现实情况。幸运的是,A2F10柱塞泵测试作为一种区分流体使用寿命的方法已经获得了广泛的关注.它比以前的产品更准确地反映了现实世界的情况,并使最终用户能够更准确地确定液压油应该在他们的设备中使用多长时间。
液压流体发展趋势
随着液压设备的不断发展,对现代液压润滑剂的要求也发生了重大变化。效率越来越成为业界关注的焦点,人们尤其关注降低TCO和增加换油间隔时间。
与此同时,由于设备要求液压油以更少的体积做更多的工作,液压油承受的压力比以往任何时候都要大。在当今的应用中,流体必须提高保护设备部件的能力,并执行其核心功能,润滑油制造商在满足这些新目标方面面临着越来越大的压力。
最后,设备控制正变得越来越数字化和自动化,这意味着液压流体在更复杂的系统中运行。这种复杂性需要额外的特性,而以前的流体迭代不一定需要这些特性。
所有这些新兴趋势都要求液压油在尽可能真实的条件下进行测试,以证明它们在这些不断变化的环境中能够在高水平上发挥作用。然而,直到最近,液压油性能的测试方案仍陷于过去的困境。
传统的测试没有达到目的
ASTM D943和ASTM D4310是用于测量液压油抗氧化性能并预测油寿命的两种最常见的台架试验。这些测试最常被液压油制造商使用,因为它们比现场试验更便宜,耗时更短。
最初,这些台架测试为最终用户提供了足够的信息,以便他们在机器中使用何种液压液时做出明智的决定。不幸的是,测试程序在预测液压油在现实世界中的表现方面存在重大缺陷。
例如,ASTM D943旨在通过记录总酸数(TAN)的变化来测量氧化电位。该试验评估了液压油在氧气、水、铜和铁的存在下,在高温下一段时间内的氧化稳定性。虽然这种方法确实揭示了一些关于油的信息,但它忽略了一个事实,即由于氧化和高TAN导致的液压油故障很少发生。事实上,大多数液压油故障是由污染引起的,这使得ASTM D943对液压油在实际液压设备中如何运行的测量无效。
类似地,ASTM D4310重复了一些与ASTM D943相同的方法错误,因为它只是原始测试的修改。它测量了在1000小时内形成的不溶性物质的重量,以及油、水和泥相中铜的总量。虽然这确实开始解释污染和油泥积聚,但在现实条件下,测试结果与石油的总体寿命之间并没有发现相关性。
对这两个台架测试的仔细检查表明,这两种传统测试都不能为最终用户提供准确的石油寿命总体情况,这就是为什么工程师们很清楚必须开发一种新的测试。毕竟,最终用户正在使用这些测试产生的信息来决定在他们的设备中使用哪种液压油。幸运的是,A2F10柱塞泵测试现在已经存在,可以提供关于整体油寿命的更好信息。
A2F10泵测试如何推动行业发展
A2F10柱塞泵测试已经存在了近20年。该测试于2004年由日本工程机械协会(JCMAS)首次引入,用于指示建筑设备中液压油的使用寿命。与其他液压泵测试不同,A2F10不测量磨损保护,而是转向测试污泥、氧化和腐蚀性能。下面是它的工作原理。
A2F10是一种弯轴轴向高压柱塞泵,通过它循环13升液压油。该流体承受的压力为每平方英寸5000磅(PSI),温度为80摄氏度(°C),速度为每分钟1500转(rpm)。将60米长的铜催化剂放置在池中,并以每小时1升(L/h)的速度向系统中添加空气,以加速氧化。研究人员定期(通常每100小时)采集液体样本,直到500小时的测试极限,每次都用7个不同的参数对它们进行评估。液压油必须在每个时间间隔内落在指定的限度内。如果在超过500小时的时间内,该流体的任何一点都超出了关键参数,则认为该流体未通过测试。
在设计测试时,工程师们创造了这样的条件:500小时的泵测试与2000小时的实际液压设备测试相对应。对于用户来说,重要的是要注意,在测试中,泄油间隔(ODI)可以被预测为通过小时的四倍。流体成功通过A2F10测试的时间越长,ODI在现实世界中的时间就越长,从而降低设备的TCO。对于某些液压油来说,这意味着它们在两次换油之间的使用时间可以长达8000小时。
实际上,更长的odi意味着更少的设备停机时间和更少的生产计划中断,这意味着更低的TCO。终端用户如果能够更准确地预测他们的设备何时需要更换,就可以更准确地预测成本,并提高他们的整体底线。
为什么重要
液压市场将继续增长和发展,因为它已经在过去十年。因此,客户对扩展odi越来越感兴趣,以降低设备生命周期内的成本。他们依赖于原始设备制造商、润滑油制造商和石油营销人员所做的测试,这些测试必须准确地反映出液体在真实条件下的表现。不幸的是,像ASTM D943或ASTM D4310这样的传统测试并不能提供适当的信息来得出关于石油寿命和在役油田性能的结论。
这就是为什么A2F10柱塞泵测试已经成为衡量现实世界结果的宝贵方法。A2F10测试的重点是测量污泥、氧化和腐蚀性能,而不是评估磨损。这些标准更密切地反映了实际液压设备中发生的情况,因此在最终用户试图决定使用哪种液压油时更有帮助。
Joshua Dickstein博士,是俄亥俄州威克利夫路博润公司的工业油技术部署经理。