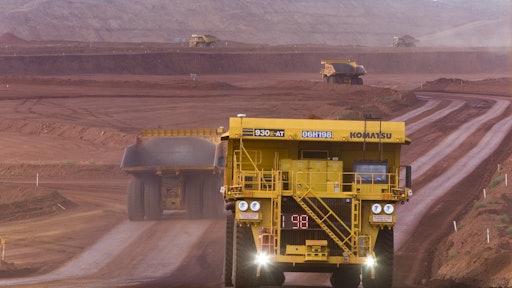
采矿一直引领着全自动驾驶汽车的发展,部分原因是它可以提供运营效率。即使是最小的改进也能给采矿作业带来很大的节省。卡特彼勒(Caterpillar)、小松(Komatsu)和沃尔沃(Volvo)等原始设备制造商多年来一直在开发和测试自动驾驶汽车技术,包括半自动和全自动汽车。
卡特彼勒公司(Caterpillar Inc.)拥有完全自主的采矿卡车车队,在西澳大利亚州的两座矿山运行,一座由必和必拓(BHP Billiton)运营,另一座由Fortescue Metals Group运营。Fortescue的矿场有45辆Cat 793F CMD卡车,这是卡特彼勒目前提供的唯一全自动商用卡车。在2016年6月的季度产品报告中,Fortescue宣布,自2013年首次调试机器以来,自动车队已经运输了2亿吨材料。
卡特彼勒还在亚利桑那州图森试验场(Tucson Proving Grounds)运营着一支小型自动驾驶卡车车队。在这个地点,该公司测试机器和自动系统的潜在软件更新,然后将它们安装到客户的运营中。
沃尔沃集团今年5月宣布了这一决定演示用于采矿作业的全自动卡车.传感器和GPS技术持续读取车辆周围环境,绕过障碍物,确保地面和地下的安全机动。它的运输系统还收集数据,进一步优化卡车的路线和交通安全。
9月7日,公司宣布已经开始测试全自动卡车在瑞典的一个地下矿井里
沃尔沃建筑设备(Volvo CE)新兴技术总监Jenny Elfsberg表示,该公司一直致力于自主轮式装载机、搬运车和挖掘机的研究项目。她说:“我们的自动轮式装载机在装卸货物时可以达到熟练操作员大约一个小时的70%的生产力水平。”轮式装载机已经在瑞典一家客户的沥青工厂进行了测试,以测试其在真实工作环境中的能力。
自动驾驶机器的控制甚至比最熟练的人工操作车辆更有效、更精确,从而提高效率,如燃油经济性、整体机器性能、生产率提高和车辆耐用性,特别是在重复任务期间。埃尔斯伯格说,未来有可能让一个操作员同时控制三到四台机器,进一步提高生产率,同时降低劳动力成本。
在自动驾驶汽车领域的工作使沃尔沃建筑设备能够开发新的创新,并将其推向市场,包括半自动和全自动功能,在实现最终目标之前,这些功能可以支持短期和中期开发。Elfsberg说:“尽管这项技术可能还需要数年时间才能投入生产,但目前取得的进展令人兴奋。”
涉及的技术
卡特彼勒目前有三种类型的自动机器在世界各地的矿场使用。这些包括半自动D11T推土机和半自动地下自卸车(LHD),以及全自动793F CMD卡车。
所有的自动机器都使用Cat MineStar系统,卡特彼勒的矿山作业和移动设备管理系统。该系统具有舰队跟踪、接近检测、远程机器操作以及半自动和全自动操作的功能。MineStar的指挥拖运功能使793F CMD卡车完全自主操作。
整个矿山的地图和所有可能的运输路线都被内置到系统中,并在卡车完成装载和倾倒循环时不断实时更新。每辆自动驾驶卡车都配备了GNSS硬件和软件,可以沿着运输道路、装载和倾倒区域进行准确引导。所有机载系统都与中央控制系统通信,操作员可以监控车队,并在必要时接管控制,例如当运输道路发生故障或堵塞时。
打滚指令是D11T推土机上采用的半自动打滚系统。这些机器一直在怀俄明州的Arch Coal Thunder Basin煤炭公司-黑雷煤矿运行;从去年8月开始,这些机器已经记录了超过25000小时的运行时间,移动了超过2300万立方码的松散材料。打盹机命令使远程操作人员可以同时控制四台推土机。一旦建立了推土机的任务,机器就会自动运行,直到任务完成。
使用该系统的好处之一是提高了安全性。通过远程控制推土机,操作人员可以在办公室环境中免受各种环境危害。机器的自动化也使它们能够运行更多的时间,因为它们不需要像人类操作员那样休息。
为了提高地下采矿的安全性,卡特彼勒开发了半自动LHDs,目前在内华达州的纽蒙特矿和世界各地的其他多个地点运行,很快也将在安大略省的矿山运行。Cat MineStar命令用于地下系统,使lhd能够自主执行装载-携带工作循环的旅行和转储阶段。与推土机类似,操作人员远程位于矿井表面,并使用远程控制来操纵机器。卡特彼勒公司表示,自动化可以使机器运行速度更快,而且由于减少了撞墙的可能性,机器的损坏几乎为零。该系统在地下工程建设中也有潜在的应用价值。
根据应用程序的不同,自动化整个工作周期并不总是可以实现或具有成本效益。LHD需要操作员远程控制,因为被装载的抛丸岩石不均匀,很难实现铲斗装载功能的自动化。在推土机的情况下,其工作环境的快速变化,需要一个远程操作员与推土机进行第一次传递,以确定在哪里开始和结束每一个传递。
作为“未来矿山”项目的一部分,矿业集团里约热内卢Tinto在其西澳大利亚州的三个地点总共运行了71台自动机器,以及7台完全自主的钻机。该项目旨在寻找高效开采和提取材料的新方法,同时减少对环境的影响,提高安全性。这些卡车运送了大约20%的作业材料。
里约热内卢Tinto使用的是配备小松自动运输系统(AHS)的小松矿用卡车。该系统由小松有限公司、小松美国公司和模块化采矿系统公司联合开发,由车辆控制器、高精度GPS、障碍物探测系统和无线网络系统组成。一台监控计算机将目标路线和速度的信息无线发送给无人矿用卡车,使其能够自主完成装载和倾倒循环。力拓公司员工在距离矿场1500公里(932.1英里)的珀斯运营中心监控自动驾驶车队。
远程控制车辆不仅可以保证操作人员的安全,还可以有效地交付货物。卡车沿着预定的路线和设定的速度行驶,消除了人工操作可能发生的波动,并对燃油效率或生产率产生负面影响。“这些新技术通过减少可变性、提高进度效率和早期识别系统瓶颈,带来了价值和生产力效益。自动卡车车队在维护、轮胎寿命和燃料方面也大大节省了,”里约热内卢Tinto中国、韩国和日本铁矿石首席执行官安德鲁·哈丁(Andrew Harding)在2014年的一份新闻稿中表示,他宣布该公司的自动卡车车队自2012年投入运营以来已经运输了2亿吨材料。
2015年9月,在一份关于其在西澳大利亚州铁矿扩张的新闻稿中,里约热内卢Tinto表示,自动化带来了显著的生产力效益和节省成本。在那里运营的自动驾驶卡车的生产率比有人驾驶的车队高12%,由于自动驾驶卡车的效率,该公司的装载和运输成本降低了13%。
该公司表示,随着生产率的提高,它已经能够更好地应对采矿业商业周期的起伏,并将自己定位为该地区成本最低的铁矿石生产商。
作为自动驾驶系统的供应商,RCT直接与原始设备制造商和最终用户合作,集成其技术。它为地面和地下采矿设备提供视距、远程和多机自动化系统。
今年3月,RCT发布了ControlMaster独立指导系统,以满足日益增长的采矿自动化技术需求,特别是在地下开采中。转向、制动和速度都由系统自动控制。RCT的ControlMaster产品经理Brendon Cullen表示,操作员设置了一个预先确定的路径,然后机器将沿着该路径运行,而不需要操作员输入。系统中使用的激光技术使机器保持在其路径的中心,并防止它撞到墙壁或其他障碍物。
该公司最近也改装其ControlMaster视距远距推土机系统在肯塔基州的一个煤矿里,一辆15年的卡特彼勒D8R上。RCT的系统使操作人员能够使用手持控制器在安全距离远程控制推土机。该系统的集成需要该公司定制几个组件。卡伦说,有必要修改电缆,并安装连杆、气缸和传感器,以使远程控制系统与机器无缝连接,而不影响其操作系统。
自主驾驶是未来的发展方向
随着采矿业寻找提高生产率和安全性的方法,特别是随着地下作业深入地表,全车辆自动化将继续在采矿业内扩展。
卡特彼勒表示,该公司正在不断改进目前可用的所有三类自动机器的操作。该公司还致力于将其他类型的矿机完全自动化。旋转爆破钻很可能是下一个完全自动化的钻机。
除了提高生产率和安全性,对熟练劳动力的需求也是采矿自动化的主要驱动力之一。多年来,寻找合格的机器操作员变得越来越困难。通过提供在更理想的位置操作自动机器的能力,例如在一个不像矿区那样偏远的位置的办公室,采矿业务将更容易吸引新员工。阿特拉斯·科普柯采矿和岩石挖掘业务部营销-自动化副总裁Brian Fox在接受公司采访时表示,与传统运营商相比,寻找能够处理数据和网络的人员将更容易,因为新一代员工接触到新技术,并接受过新技术的教育。
福克斯表示,虽然自动驾驶汽车的操作越来越普遍,而且预计在可预见的未来还会增长,但采矿业没有像制造业等行业那样迅速适应自动化,其中一个原因是机器工作的地质和环境条件不断变化。此外,客户的需求并不大。虽然安全对他们来说很重要,但该行业在制定安全程序和法规方面做得很好。然而,他表示,该行业现在已经到了一个需要自动化才能实现进一步改进的阶段。
Cullen指出,在采矿中集成自主控制的限制之一是现有场地上机器和人员的相互作用。他说:“在可预见的未来,采矿过程的一些功能仍然需要人工控制。”“虽然大多数自动机器在发生计划外移动时都有许多安全措施,但机器不能总是控制它与人类控制的机器和车辆的交互。”
他补充说,虽然与现有矿区的整合存在挑战,但如果一个矿山是围绕自主控制设计的,那么这些挑战可以在矿山规划阶段克服。
合理的成本和确保自动驾驶技术的可靠性也是阻碍更广泛采用的因素。随着长期测试的结果越来越多,这些系统的开发和测试也在不断增长,自动驾驶汽车也将出现在采矿作业中。