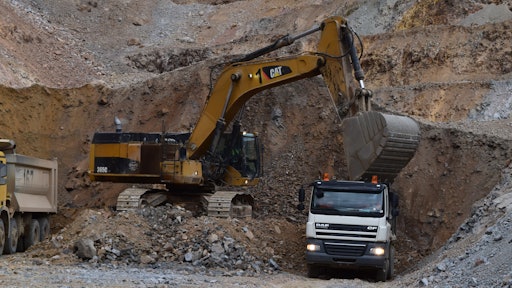
对于任何产品开发活动来说,知道你想要去哪里以及如何到达那里是至关重要的。虽然这些因素和其他因素是新产品或重新设计产品的重要驱动因素,但它对公司利润的影响也是如此。在产品开发过程中,验证是降低潜在风险的关键。
从相对简单的重新设计到新产品的推出,公路上和非公路设备制造商必须权衡许多因素。
- 快速上市可以更快地收回开发成本,但牺牲了质量吗?
- 创新有多重要?验证多个设计需要投入多少时间/金钱?
- 我们是否拥有验证设计所需的工具/技术能力?
- 保修索赔是否超出预期限度?
- 验证成本是最重要的问题吗?
- 必须考虑哪些新的或即将出台的法规?
基本验证方法
今天,有两种基本的方法来验证与设备或特种车辆相关的产品。每一种都是经过验证的、有效的和技术上合理的,并有其优点:
- 以测试为中心的验证——通过物理原型的测试进行验证
- 以模拟为中心的验证——通过测试数字原型进行验证
这并不是说物理测试和模拟是相互排斥的。许多较大的组织同时采用这两种方法。事实上,任何合法的产品验证方法都应该包含每一种方法的元素。
Test-Centered验证
以测试为中心的耐久性验证植根于在车辆/设备投入运行时捕获和分析物理性能数据。通过在车辆上安装应变计和加速度计来收集数据,以测量挠度或量化系统、子系统或组件在负载和条件下的反应。
数据通过多种方式收集,从受控的实验室环境,代表性的环境,或在典型操作条件下的现场。测试因系统、子系统或组件验证而异。
以测试为中心的验证提供了物理上看到、触摸和测量被验证产品的优势。
六D测试与分析
系统级持久性验证
在系统层面(以及某些子系统),液压试验台可以在实验室或受控环境中重现使用条件。以系统级测试为中心的验证通常有两种形式:耐久性测试和扩展操作测试。
耐久钻机试验
系统级耐久性测试通常使用实验室中的液压试验台。这需要使系统在很长一段时间内受到外力的影响,重新创造现场条件。这样就可以在相对较短的时间内衡量长期影响。
有限元分析(FEA)确定应变计和加速度计的位置。来自基线测试的负载和响应定义了运行环境和相关的耐久性参数。该过程转移到驱动文件的开发,以控制测试平台,重新创建系统将受到的力。在测试台上完成测试后,系统会被检查是否有裂缝和其他结构损坏。
扩展运行测试
另一种流行的验证方法是在有代表性的环境中对系统进行持续操作和测试。这包括一个测试轨道,试验场,现场使用等。与液压钻机测试类似,通过测量应变和加速度来确定加速损伤的程度。分析大量积累的数据提供了洞察产品性能和客观验证设计的手段。
子系统和组件验证
当从系统中分离出来时,每个子系统或组件可以按设计执行。但是有时,当并入系统时,与相邻组件/子系统的交互会引入意想不到的力或振动,而组件/子系统的设计并不能承受这些力或振动。
为了测量系统环境中的性能,力和/或加速度从系统级测试中获得。在测试组件或子系统时,使用液压或电动激振器复制这些力。
优势
以测试为中心的验证的一个优势是能够实际地看到、触摸和测量正在验证的产品。与此同时,现场测试允许对产品进行验证,不仅针对预期的客户使用情况,而且针对预期操作范围之外的异常和其他罕见事件。这使得车辆/装备设计可以满足一系列的可能性。
缺点是,复杂的加载不容易应用于试验台测试。此外,物理测试多个原型可能是耗时、劳动密集型和昂贵的。对于卡车应用,还必须考虑与钻机、轨道时间、人工、设备以及建模和分析相关的成本。因此,以测试为中心的持久性验证方法通常用于大批量、高价值、高风险的情况。
在设计车辆或设备时,选择正确的验证过程有助于减少保修索赔,同时确保满足所有设计要求。
六D测试与分析
以模拟为中心的验证方法
虽然以模拟为重点的方法严重依赖于FEA,但仍然需要物理原型测试,尽管能力非常有限。尽管如此,与以测试为中心的验证相比,这种数字方法是快速、可靠和廉价的。
测试数据(通常来自竞争对手的品牌)提供了近似的加载环境。对于卡车和非公路设备,这可能包括通过无人值守测试从现场收集数据。通过长期收集数据,可以了解在服务期间可能遇到的常见和罕见(但重要)负载。
一个人越了解客户将如何使用产品,包括负载和响应机制,模拟就越有效。模拟效果越好,返工、时间损失和成本就越少。
数据收集与分析
有效的FEA模型验证需要对模型施加代表性的、比例的和极端的(合理的)力。这确保了模型根据最终产品将受到的准确操作参数进行评估。
这些力量是通过测试物理原型、当前模型或竞争车辆手动收集的。这通常包括在整个飞行器的关键位置安装加速度计和应变计,并使设备投入使用。建议在正常使用和试验场测试时同时收集数据。通过这种方式,力、加速度、扭转、俯仰和应变都被测量到每个关键位置。
在下一阶段,现场测试数据将与现场或试验场收集的数据进行比较,以确定加速耐久性测试周期。将测压元件的数据与应变响应进行比较,以确定代表车辆使用情况的重要载荷情况。这些载荷情况(例如,车身扭曲、节距、应变等)是基于损伤计算进行排序的。同样地,验证地面数据与现场测试载荷案例相关联,并根据损伤计算进行缩放。根据这些比较,定义了一组加速耐久性试验场地项目并进行了排名。
使用工程分析(仿真)软件进行加速耐久性仿真。这有助于预测地面测试性能。静态和惯性载荷案例是根据现场和验证地面数据开发的。这包括荷载情况与实测应变响应的关联,有助于阅读有限元模型相关活动。
虽然静态有限元分析可能已经足够了,但测试结果有时表明需要处理系统动力学。在这些情况下,将创建一个动态模型,预测显著的低频振动模态,并与模态测试相关。
优势
以模拟为中心的验证加速了产品开发并增加了创新。通过建模和仿真评估设计更改,可以快速探索多个设计迭代,而无需构建和测试大量物理原型的时间和费用。受上市时间或创新驱动的组织或预算有限的组织将受益于这种方法。
什么方法是最好的?
这些验证方法同样有效;虽然两者都包含测试和模拟的元素,但验证的重点和路线图是非常不同的。花点时间仔细检查可用的验证资源,确定业务驱动因素,权衡每种方法的利弊。
本文由Six D测试与分析的业务开发经理Robert Hales贡献
作者简介
鲍勃·黑尔斯是公司业务发展经理六D测试与分析(6 d)。6D为产品生命周期的所有阶段的机械工程挑战提供了答案。从上游设计验证到现场测试、故障排除和下一代产品开发,6D帮助客户在产品创新、质量、可靠性和性能方面实现可衡量和持续的改进。